You walk into your Shopify dashboard and see: missing stock numbers, products showing as unavailable when they’re in the warehouse, or orders failing because inventory isn’t tracked properly. These are symptoms.
The cause? Inventory tracking not being enabled or syncing issues across locations.
Without proper tracking, inventory management turns into a trial-and-error process, leading to overselling, stockouts, and frustrated customers. Keeping inventory records aligned with actual stock levels ensures smooth order fulfillment and a better shopping experience.
This guide breaks down what "inventory not tracked" means in Shopify, why it happens, and how to fix it.
What does ‘inventory not tracked’ mean in Shopify?
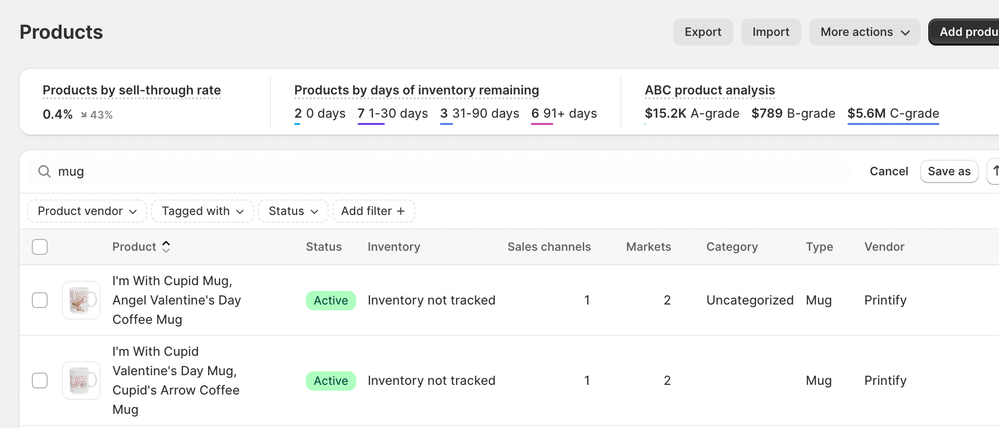
When Shopify shows inventory not tracked, it means the system isn’t keeping count of stock levels for that product. You can keep selling without worrying about stock running out, but Shopify won’t stop orders even if the item is unavailable. If you rely on inventory updates to manage your products, this can lead to problems.
There are times when disabling inventory tracking makes sense. If you sell digital products, services, or custom-made items, there’s no need to track stock.
Print-on-demand and dropshipping models also don’t always require Shopify to monitor inventory since suppliers handle fulfillment.
However, leaving inventory untracked can cause issues. If a product sells out and Shopify still accepts orders, customers might buy something that isn’t actually available. This can lead to delays, refunds, and frustration.
If customers keep running into unavailable products, they might lose trust and shop elsewhere.
Diagnosing the main problems behind 'Inventory Not Tracked'
If you’ve been seeing ‘Inventory Not Tracked’ or inventory is not tracked at any location on Shopify for your products, here are a few things to check
No. 1: Checking product settings for inventory tracking status
Go to your Shopify admin and open the product page. Scroll to the Inventory section and check if ‘Track Quantity’ is enabled. If this box is unchecked, Shopify will not monitor stock levels.
For products with multiple variants, review each one separately since they have individual inventory settings.
No. 2: Assessing third-party app integrations for inventory discrepancies
If you use external apps for fulfillment, inventory tracking might be controlled outside of Shopify.
Some apps automatically sync stock levels, while others require manual updates. If Shopify shows inventory is not tracked but you expected it to be, check the settings in the fulfillment app you use.
If there’s a mismatch between Shopify and the external system, inventory tracking may not work correctly. Disconnecting and reconnecting the integration or updating stock settings within the app may help resolve the issue.
No. 3: Exploring Shopify settings that might affect inventory tracking
Shopify has settings that can override inventory tracking. If ‘Continue selling when out of stock’ is enabled, Shopify will keep accepting orders even when stock runs out. This can make it seem like Shopify inventory is not tracked at all. Check this setting under the Inventory section for each product to ensure it aligns with how you want to manage stock.
Step-by-Step Guide to Fixing 'Inventory Not Tracked'
Here are a few possible solutions for how to change inventory not tracked on Shopify
1. Enabling inventory tracking for individual products
Navigating to product settings
Go to your Shopify admin and click on Products. Find the product you want to update and click on it to open the product details page. Scroll down to the Inventory section to check its current tracking status.
Setting up inventory tracking options
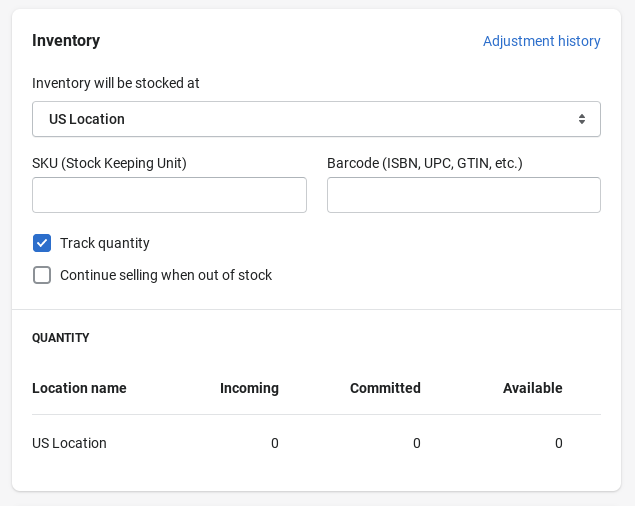
In the Inventory section, look for the ‘Track quantity’ checkbox. If it’s unchecked, Shopify is not tracking inventory for this product. Check the box to enable tracking, then enter the correct stock level. If you want Shopify to stop selling when the stock reaches zero, make sure “Continue selling when out of stock’ is unchecked. Click ‘Save’ to apply the changes.
2. Batch updating inventory settings for multiple products
Using Shopify's bulk editor
If you need to enable tracking for multiple products, go to Shopify admin > Products and select the items you want to update. Click ‘Edit Products’ to open the bulk editor. Find the ‘Track quantity’ column and check the boxes for all selected products. Adjust stock levels if needed, then click Save to apply the updates.
Importing CSV files for mass updates
For larger product catalogs, Shopify allows bulk updates via CSV import. Go to Shopify admin > Products > Import and download the sample CSV file. Update the Variant Inventory Tracker column with "Shopify" for all products that need inventory tracking. Upload the updated file and let Shopify process the changes.
3. Ensuring integrations are properly configured
Checking app permissions and settings
If a third-party app controls inventory, go to Shopify admin > Apps and open the relevant app’s settings.
Look for inventory management options to confirm whether the app is tracking stock instead of Shopify. If Shopify’s settings seem incorrect, the app might be overriding them.
Re-syncing inventory data between Shopify and apps
If inventory levels don’t match between Shopify and an integrated app, a resync may be needed. Open the app’s dashboard and look for a Sync inventory or Update stock option. Manually syncing the data can also resolve mismatches and ensure Shopify displays the correct stock levels. If issues persist, disconnecting and reconnecting the app may reset the integration.
Prediko’s inventory management app syncs with your Shopify store inventory with a click and gives you a real-time data view for making educated stock-related decisions.
4. Seeking support from the Shopify community and support channels
If troubleshooting on your own doesn’t resolve the problem, Shopify’s support resources can provide additional help.
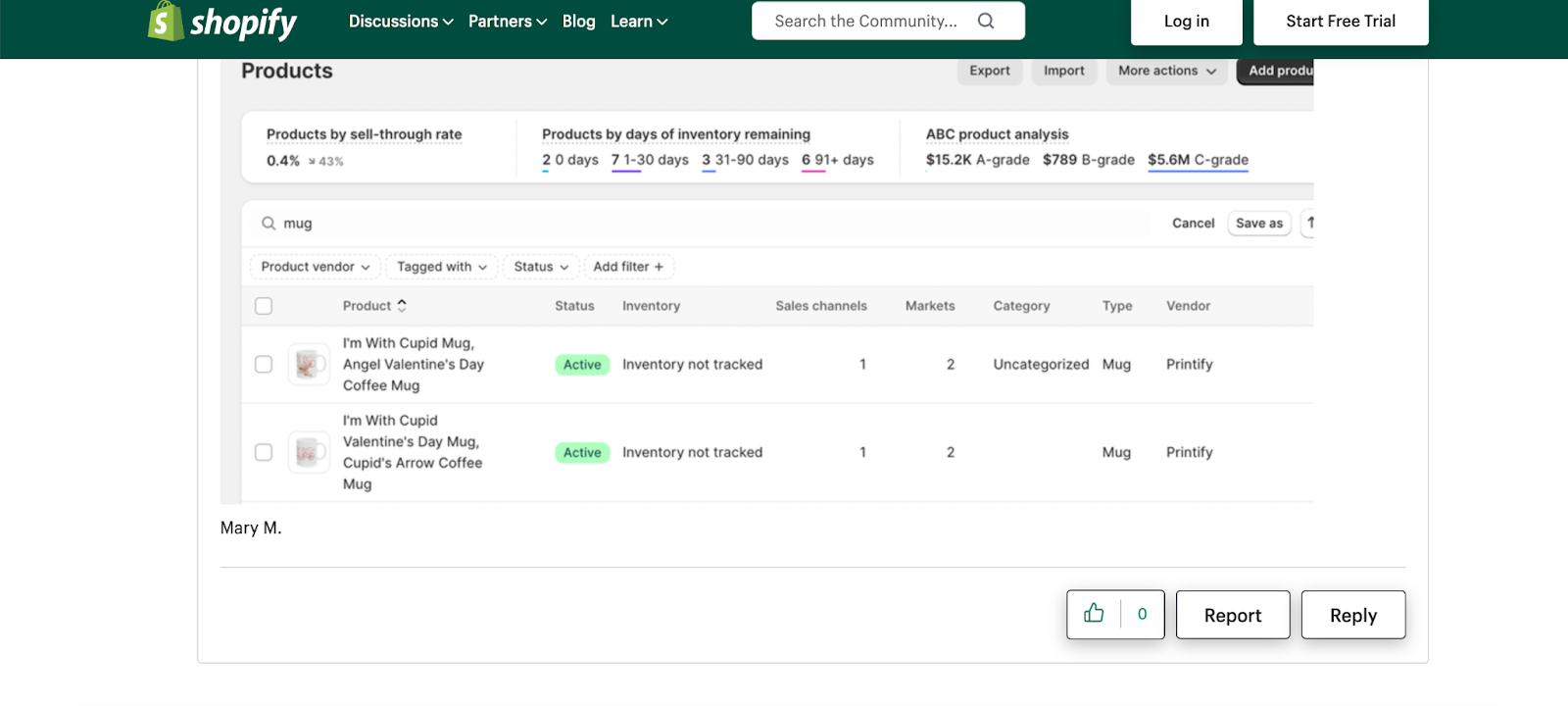
- Search Shopify Community Forums to see if others have experienced similar inventory tracking issues
- Contact Shopify Support for direct assistance with settings, sync errors, or unusual inventory behavior
- If the issue is related to a third-party service, reach out to the provider’s support team for troubleshooting steps
Reaching out to support can help uncover settings or integration conflicts that may not be immediately obvious in your Shopify dashboard.
Best Practices for Inventory Management in Shopify
Now that you know how to fix the inventory not tracked issue, here are some best practices you can follow when managing inventory in Shopify
1. Regularly auditing inventory settings and levels
Inventory tracking isn’t something you set once and forget. Shopify settings, third-party apps, and even accidental changes can affect how your stock is managed. Checking in on your inventory settings regularly helps catch mistakes before they become major problems.
- Go through your product list and make sure ‘Track quantity’ is enabled for items that need stock monitoring
- If you use multiple variants, check that each one has the correct settings
- Look at ‘Continue selling when out of stock’ to ensure it’s only enabled for products where it makes sense
It’s also a good idea to compare what Shopify shows with your actual stock levels. If you’re using a warehouse, fulfillment service, or manual tracking, make sure everything lines up.
Small discrepancies can turn into bigger issues if left unchecked. A quick audit every few weeks helps keep things running smoothly.
2. Using tools like Prediko for advanced inventory management
There are third-party apps available in the Shopify App Store to help you better manage your Shopify inventory.
Prediko is an AI-powered inventory management tool that helps you plan, manage, and track your stock without extra hassle. It analyzes past sales, seasonality, and market trends to predict demand, so your best-sellers don’t run out and you’re not stuck with inventory that just sits there.
You also get live purchase order recommendations, low-stock alerts, and inventory health status. No more manually tracking stock levels or figuring out when to reorder. Prediko tells what your Shopify store actually needs, factoring in sales forecasts, lead times, and safety stock.
3. Setting up alerts for low stock or inventory issues
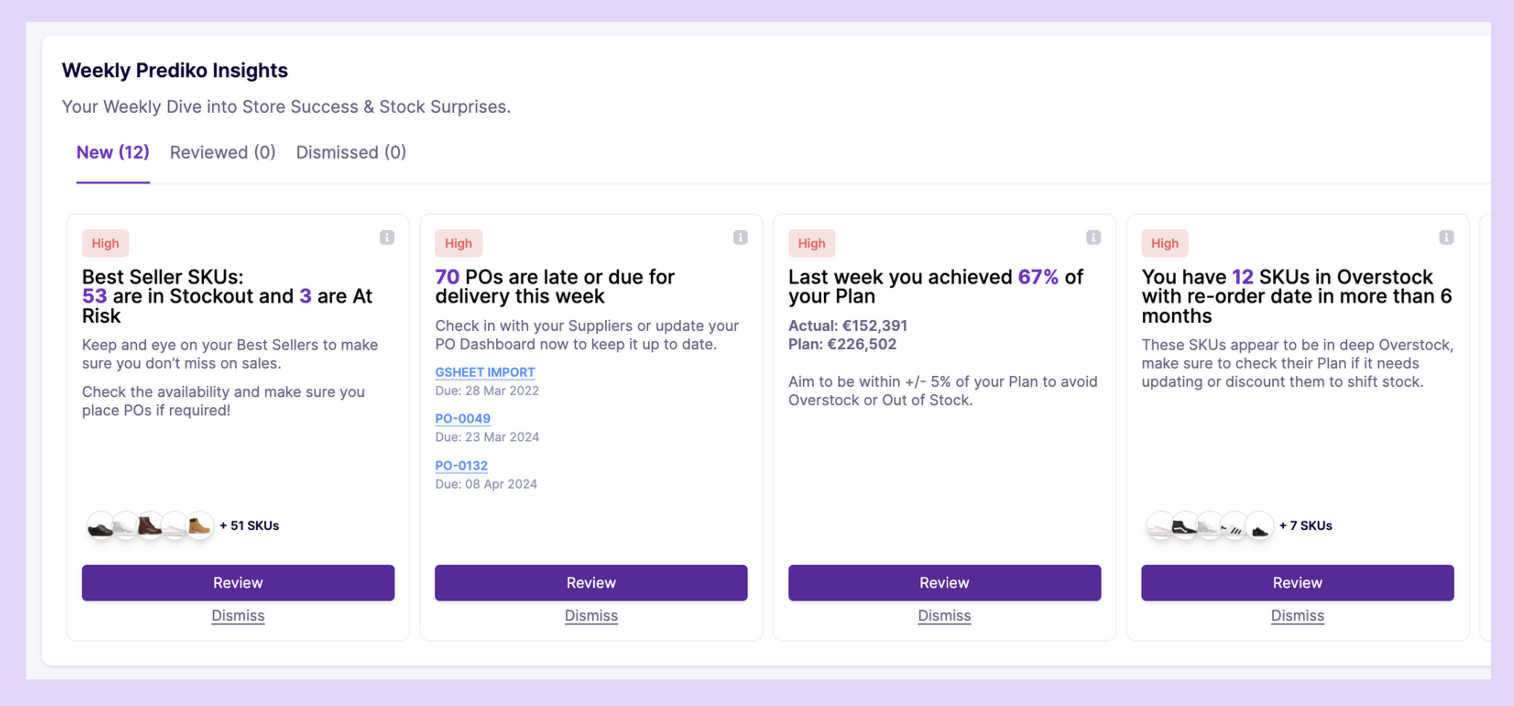
Keeping track of inventory manually can seem like sand slipping away from your hands, especially if you have a lot of products. Setting up alerts helps you stay on top of stockouts or at-risk inventory before they lead to lost sales and dissatisfied customers.
Integrate your Shopify store with tools like Prediko that allow you to monitor low-stock products and set up real-time alerts when inventory is below a defined threshold. The app doesn’t just notify you but also provides recommendations on what to order, how much, and when so that you’re not stuck with lengthy calculations.
Automated alerts make it easier to restock on time and avoid disappointing customers with out-of-stock items. Instead of constantly checking inventory, you get notified when it’s time to take action.
4. Build safety stock
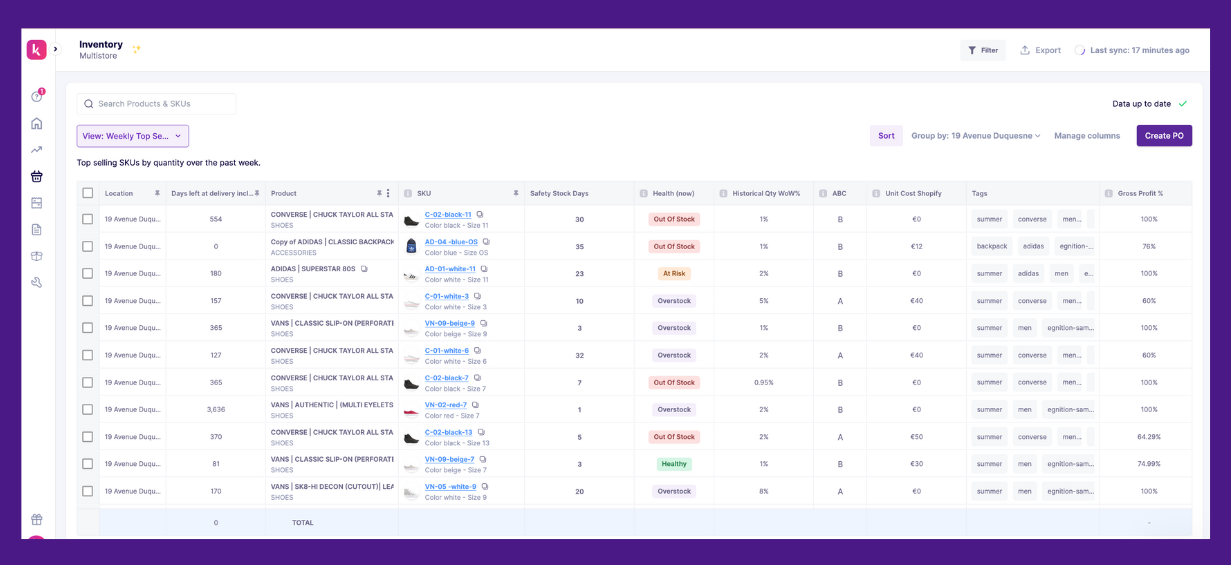
Running out of stock leads to lost sales and customers moving to your competitors. Keeping a safety stock i.e. extra inventory set aside as a backup helps prevent stockouts, especially if there are supply chain delays or unexpected spikes in demand.
- Calculate how much extra stock you need based on sales trends and supplier lead times
- Adjust your reorder points so you restock before hitting critical levels
- Monitor seasonal demand changes and increase safety stock during high-sales periods
Having a buffer means you won’t have to struggle for restocks or risk overselling.
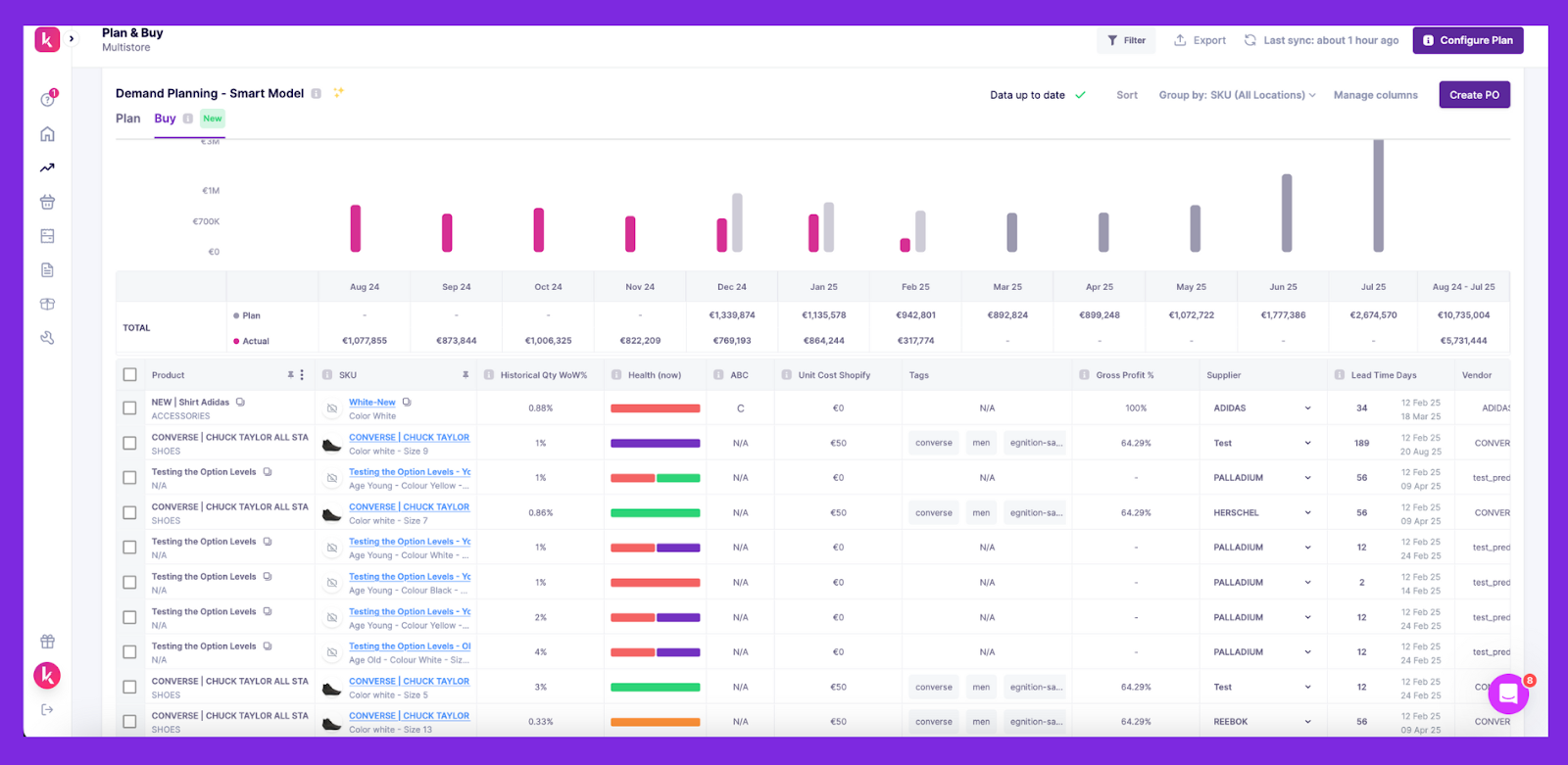
With Prediko’s AI-powered demand planning you can plan your safety stock accurately. You can analyze historical sales trends, seasonal patterns, and even promotional impacts to estimate how much safety stock you’ll need.
Instead of relying on gut feelings or static formulas, you get dynamic forecasts that adjust to your store’s unique patterns, ensuring your safety stock buffers are just right.
Also, read this complete guide on how to establish accurate Shopify safety stock levels
Troubleshooting Other Common Inventory Tracking Issues
Inventory tracking issues can disrupt order fulfillment and create stock discrepancies. Here’s how to fix other common inventory tracking problems.
1. Resolving integration conflicts with third-party apps
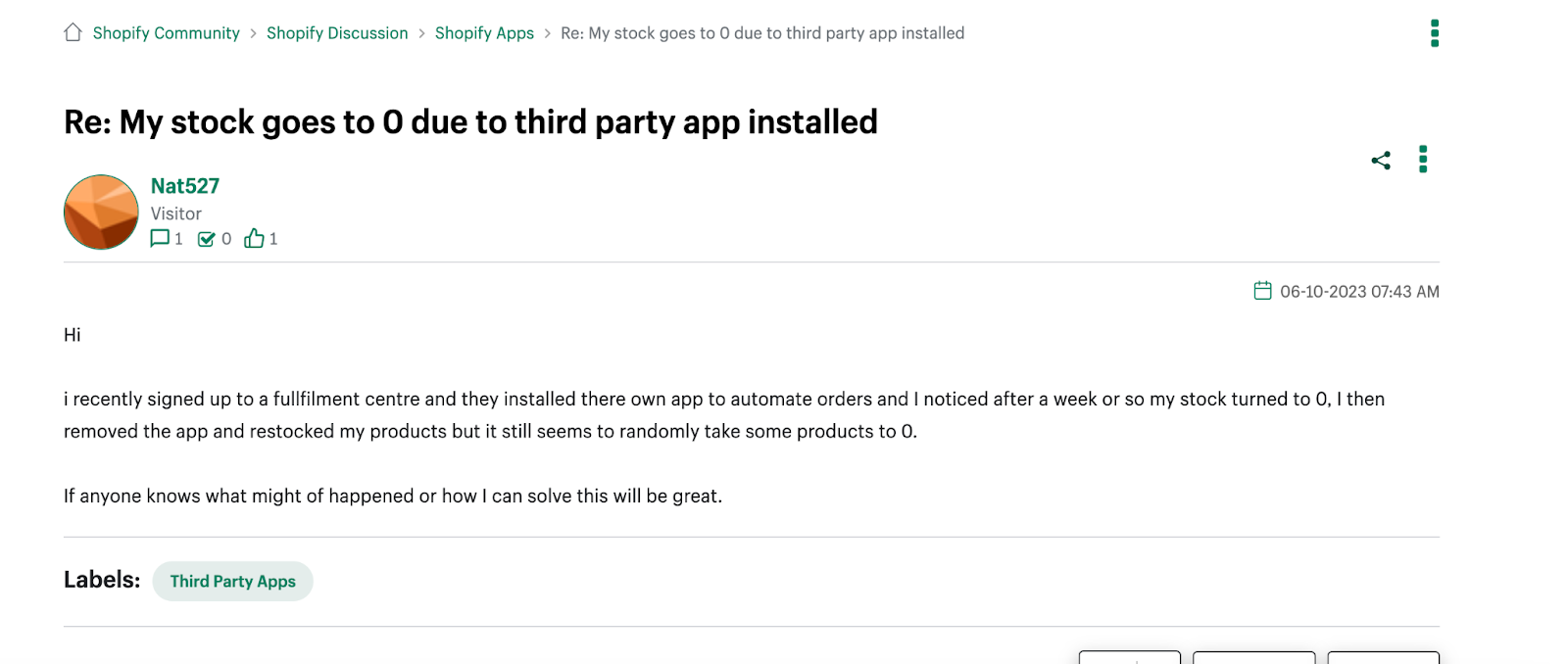
Your inventory numbers/status may get skewed because third-party inventory apps can sometimes override Shopify’s default tracking settings, leading to mismatched stock levels.
If inventory updates aren’t syncing correctly, check the app’s permissions and settings to ensure it’s configured to communicate with Shopify.
Re-syncing inventory data or disabling conflicting settings in the app can often resolve these issues. If problems persist, contacting the app’s support team or Shopify’s customer support can help identify conflicts.
2. Addressing zero stock or incorrect inventory messages
Sometimes a product shows zero stock or incorrect inventory levels when it shouldn’t. Start by verifying stock settings in Shopify. Make sure the product is set to track inventory and that the correct location is assigned.
Check for any unfulfilled orders that might be reserving stock, as this can cause discrepancies. If using an external inventory app, force a manual sync to update stock levels.
When these steps don’t resolve the issue, reviewing recent inventory adjustments in Shopify’s history can help track down the source of the problem.
How to Future-Proof Your Inventory Management?
Inventory keeps changing, and your approach to managing it should keep up.
Here are some tips to stay prepared.
1. Anticipating changes in Shopify's inventory features
Shopify constantly updates its platform, which means inventory management tools and settings may change over time.
Staying informed about these updates helps prevent disruptions and ensures you’re using the latest features to track stock efficiently.
- Keep an eye on Shopify’s changelog and announcements for any inventory-related updates
- Review new settings or changes in the Shopify admin panel after major updates
- Test new features on a small scale before applying them across your entire store
- Follow Shopify’s blog and community discussions to stay informed about new strategies
Small changes in Shopify’s inventory system can impact tracking and order fulfillment, so regularly checking for updates is important.
2. Staying updated with new tools and technologies
eCommerce inventory management is always evolving, and new tools can help streamline stock tracking and fulfillment.
Whether it's automation, AI-driven forecasting, or improved reporting, keeping up with advancements can improve efficiency.
- Explore new inventory management apps that integrate with Shopify to simplify stock tracking
- Look into AI-powered demand forecasting tools to predict inventory needs more accurately
- Use automation to reduce manual inventory updates and prevent errors
Adopting the right tools early, like Prediko, helps maintain accurate inventory records and reduces the risk of stockouts or overselling.
Prediko connects with your Shopify store in a click and pulls all the sales and inventory data.
It offers real-time inventory tracking across stores and warehouses, automated low-stock alerts, purchase order management, and AI demand forecasting, so you always have an action plan to keep accurate stock on hand.
3. Continuous learning and audits for effective inventory control
Managing inventory requires more than just the right tools. It involves staying open to emerging industry trends and adapting your approach as they evolve.
By staying informed and regularly evaluating your processes, you can ensure long-term success.
- Keep your knowledge up-to-date with online courses, webinars, and industry reports on inventory trends and strategies
- You can’t simply set and forget your inventory management processes. Conduct regular audits of your processes to pinpoint areas that need improvement or upgrade like automating error-prone manual workflows
- Adapt to changes in Shopify, new technology, and shifting customer expectations to position yourself as a forward-thinking brand.
Using Prediko to Manage Inventory for your Shopify Store
If your Shopify shows "inventory not tracked" when you need real-time visibility, it can lead to stockouts, overselling, or failed orders due to inaccurate stock levels.
Once this is fixed, you can integrate your Shopify store with Prediko’s app that automates tracking, providing real-time stock visibility across sales channels and warehouses, and low-stock alerts, so you always stay updated on your stock levels.
With AI demand forecasting and automated purchase order recommendations, you can also plan and execute restocking well in advance.
Take control of your inventory and keep your Shopify store running smoothly. Use Prediko’s AI-powered solution FREE for 14 days and start tracking your stock with confidence.
FAQs
How do I enable inventory tracking for my products in Shopify?
To enable inventory tracking, go to your Shopify admin, navigate to Products, select a product, and scroll to the Inventory section. Check the box for “Track quantity,” set your initial stock level, and save. Repeat for each product or use bulk editing for efficiency.
Why is my inventory not being tracked correctly in Shopify?
Inventory might not track correctly due to manual errors, app conflicts overriding updates, unprocessed sales, or syncing issues with third-party apps.
What are the consequences of not tracking inventory in Shopify?
Without tracking, you risk overselling (leading to canceled orders and upset customers), stockouts (missed sales), or overstocking (tied-up capital and storage costs). It also hampers forecasting and decision-making.
How can I troubleshoot inventory tracking issues in Shopify?
Enable tracking by checking “Track quantity” in product settings or bulk edit multiple items via Shopify’s editor or CSV import. Ensure third-party apps are correctly synced, resync data if needed. If issues persist, consult Shopify Community Forums or contact Shopify Support.