What is Cost of Goods Manufactured (COGM)?
The cost of goods manufactured is total production cost of the goods that a company completes during a specific period. It includes materials, labor, and overhead costs associated with the production process.
How to Calculate Cost of Goods Manufactured (COGM)?
- Calculate Direct Materials: Start by calculating total cost of raw materials used in production. This includes all materials that are directly incorporated into the finished product.
- Add Direct Labor: Include the cost of labor directly involved in the manufacturing process.
- Include Manufacturing Overhead: Add all indirect costs associated with production, such as utilities, depreciation, and maintenance expenses related to the production facilities.
Learn how to find the direct raw materials that are used in D2C brands with real examples.
How Prediko Simplifies Cost of Goods Manufactured (COGM)?
Within Prediko, you can easily track your entire raw materials catalogue by doing a simple import. Once you have imported the raw materials, you can track
1. Consumption of Raw Materials: Number of units in stock, in production, lead time and MOQ type.
2. Add and track Bill of Materials (BOM)- Select the main product, SKUs, raw materials and production time.
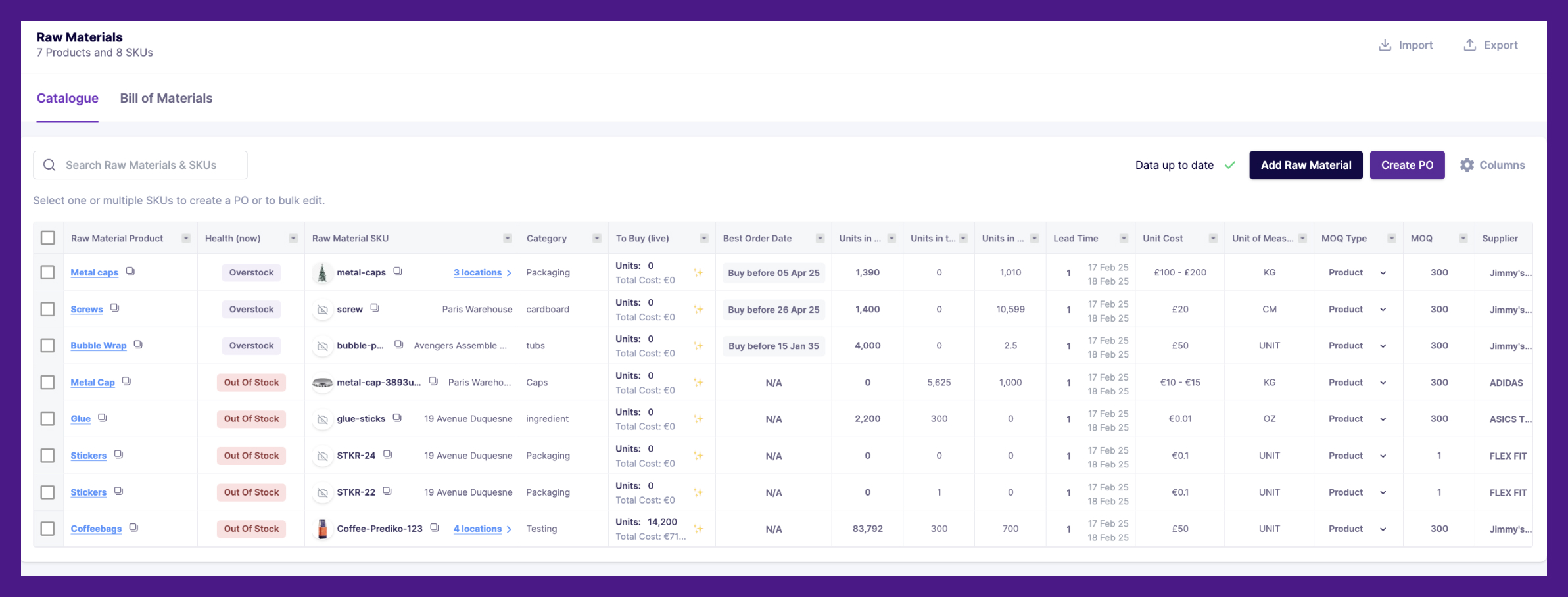
Formula for calculating Cost of Goods Manufactured (COGM)
Once you are able to track your raw materials, you can stay on top of your raw materials cost. Once you know your raw materials cost, you can easily calculate your Cost of Goods Manufactured by using a simple formula.
Calculate COGM = Direct Materials + Direct Labor + Manufacturing Overhead
There are two ways to calculate ending inventory
1. Calculate Ending Inventory Using FIFO
2. Calculate Ending Inventory Using LIFO
Cost of Goods Manufactured (COGM) schedule
The Cost of Goods Manufactured (COGM) schedule is a detailed financial report that calculates total production costs incurred by a manufacturing company during a specific period.
It provides comprehensive view of the costs associated with producing finished goods, which is essential for assessing production efficiency and determining the cost of goods sold (COGS).
Formula
COGM = Beginning WIP Inventory + Total Manufacturing Costs − Ending WIP Inventory.
Purpose and importance of COGM Schedule is for
- Financial Reporting: It provides necessary data to calculate the COGS, which is reported on the income statement.
- Cost Control: By analyzing each component, management can identify areas where costs can be reduced.
- Pricing Decisions: Understanding production costs helps in setting appropriate sales prices to achieve desired profit margins.
Example:
Consider a Shopify brand with following data for January:
Beginning Raw Materials Inventory: $10,000
Purchases of Raw Materials: $50,000
Ending Raw Materials Inventory: $8,000
Direct Labor: $30,000
Manufacturing Overhead: $20,000
Beginning WIP Inventory: $5,000
Ending WIP Inventory: $7,000
Calculation:
Direct Materials Used: $10,000 (Beginning RM) + $50,000 (Purchases) - $8,000 (Ending RM) = $52,000
Total Manufacturing Costs: $52,000 (Direct Materials Used) + $30,000 (Direct Labor) + $20,000 (Overhead) = $102,000
COGM: $5,000 (Beginning WIP) + $102,000 (Total Manufacturing Costs) - $7,000 (Ending WIP) = $100,000
Thus, the Cost of Goods Manufactured for January is $100,000.
Analysing Cost of Goods Manufactured (COGM) for Shopify D2C Brands
Compare your Cost of Goods Manufactured with industry standards or with similar companies. This helps in understanding whether the costs are reasonable or if there are opportunities for improvement.
Analyze which components of the Cost of Goods Manufactured (materials, labor, overhead) are contributing the most and target those areas for cost reduction efforts. A low Cost of Goods Manufactured also means the use of inferior materials and/or cheaper labor, which affects product quality and brand reputation.