In the world of manufacturing and production, raw material inventory management is a critical task. It's the backbone of efficient operations, directly impacting cost reduction and production efficiency.
What is Raw Materials Inventory?
Raw materials inventory is the total cost of a manufacturer's components, subassemblies, and supplies in stock that are not in production. This includes both direct materials (DM) and indirect materials (IM) essential for manufacturing a final product.
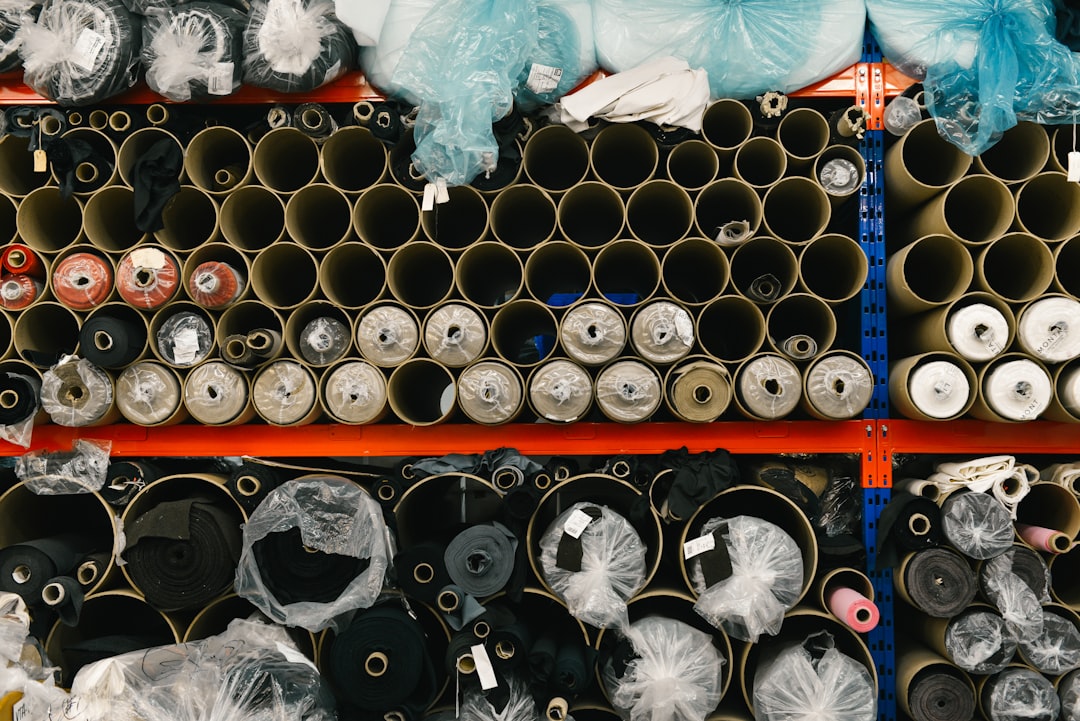
A proper raw materials inventory management is important for efficient production processes and cost control. There are two types of raw materials:
1. Direct Materials
Direct materials are components or substances that are used in the final product and can be easily traced to it. These direct materials are a part of the finished product and constitute a significant portion of the product's cost. Examples of direct materials include raw materials like wood in furniture manufacturing, steel in car production, or fabric in clothing manufacturing.
2. Indirect Materials
Indirect materials are materials that are essential for manufacturing a final product but are not directly incorporated into the end product. These materials do not become part of the final product but are necessary for the production process. Examples of indirect materials include lubricants, cleaning supplies, gloves, and other items used in the manufacturing process but not physically present in the final product.
What is raw materials management in the context of Shopify brands?
Raw materials management in the context of Shopify brands refers to the process of overseeing sourcing, procurement, and utilization of raw materials needed for manufacturing products sold by Shopify brands.
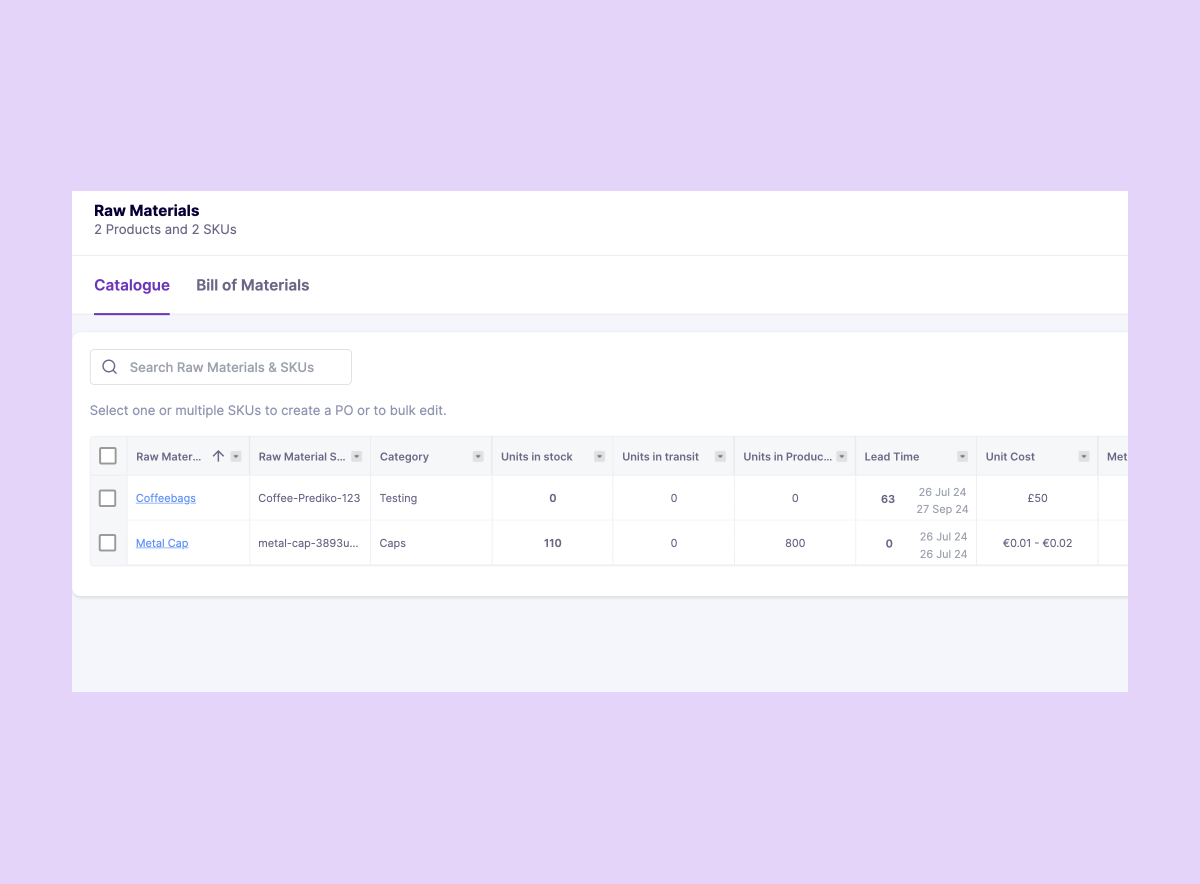
This includes activities such as inventory control, supplier management, cost optimization, and ensuring the availability of necessary materials to meet production demands. Efficient raw materials management is crucial for Shopify brands to maintain product quality, control costs, and meet customer demand.
Why is efficient raw materials management essential?
Raw material inventory management is crucial for businesses for several reasons. Efficient raw material inventory management can lead to significant cost savings. By avoiding overstocking, businesses can reduce storage costs and prevent capital from being tied up in unused materials.
Moreover, raw material inventory management impacts the financial health of a business. It ties up capital, and poor management can lead to unnecessary costs. That's why it's really important for businesses to properly manage raw materials.
Effective raw material management also plays a role in maintaining quality standards. It ensures that the best materials are used, contributing to the production of high-quality products. Whether you're a supply chain manager, a procurement professional, or a business owner, you'll find valuable information in this guide to help you optimize your raw material inventory management process.
In addition, efficient management can contribute to sustainability efforts. By reducing waste and optimizing the use of materials, businesses can minimize their environmental impact.
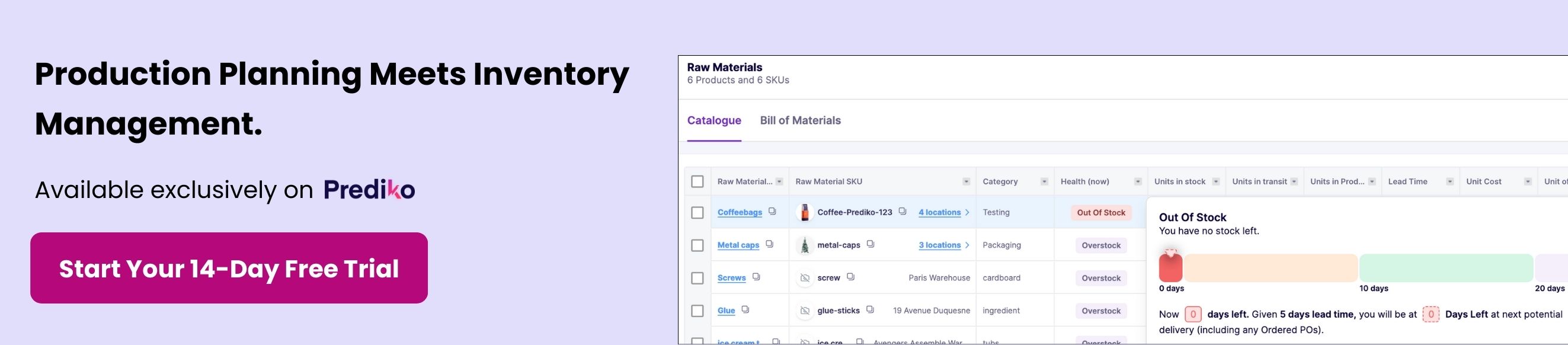
Importance of raw materials management from the POV of Shopify brands
Shopify brands can benefit a lot from a proper raw materials management process. First of all, raw materials management helps in maintaining product quality by ensuring that the right materials are available in the right quantities at the right time. This can lead to consistent product quality and customer satisfaction.
By managing raw materials efficiently, Shopify brands can meet customer demand more effectively, leading to improved customer loyalty and increased sales.
Common challenges in managing raw materials
1. One of the common challenges faced by Shopify brands is overstocking. This occurs when businesses order more materials than needed, leading to increased storage costs and tied-up capital.
2. The second key challenge is stockouts. This happens when businesses run out of materials, causing production delays and potential loss of sales.
3. Accurate demand forecasting is another challenge. Predicting the exact amount of raw materials needed can be difficult, especially in volatile markets.
How to be efficient in raw materials management?
Enter raw material inventory management software. A good software can help in streamline the entire process, making it easier to compute, track, and record raw material inventory.
These features ensure that the software can handle complex operations and scale with your business. So how do you choose the right software for your needs? What features should you look for? And how can you leverage this technology to its fullest potential?
Key features of raw material inventory management software
When evaluating inventory management software, there are several key features to look for:
- Automation: This can help you in saving time and reducing errors by automating tasks like data entry and calculations.
- Reporting & analytics: Reporting provides valuable insights into inventory performance and trends. They help businesses make informed decisions and improve their inventory management practices.
- Scalability: This is another important consideration. The software must be able to handle the number of inventory units that you have within the brand.
- User-friendly interface: The software should be easy to use and navigate, ensuring that all users can effectively utilize its features.
It’s very difficult to find a software that has all these features especially when handling a large number of raw materials for a particular Shopify brand. We have also created a list of top raw materials inventory management apps.
How Prediko helps Shopify brands overcome challenges
Prediko offers several key features to help Shopify brands manage raw materials effectively:
1. Real-time Tracking: Prediko provides up-to-date information on inventory levels across multiple warehouses and locations. This feature allows businesses to respond quickly to changes in demand and maintain steady production flows. By knowing exactly what materials are on hand, businesses can avoid overstocking and stockouts, ensuring a smooth production process.
2. Improved Forecasting and Demand Planning: With advanced data analytics tools, Prediko integrates raw material data with production schedules and sales forecasts to provide a holistic view of demand. The system uses historical sales data to predict future demand, helping businesses plan their raw material needs more effectively. This integration ensures that companies have the right materials at the right time, reducing the risk of overstocking or stockouts.
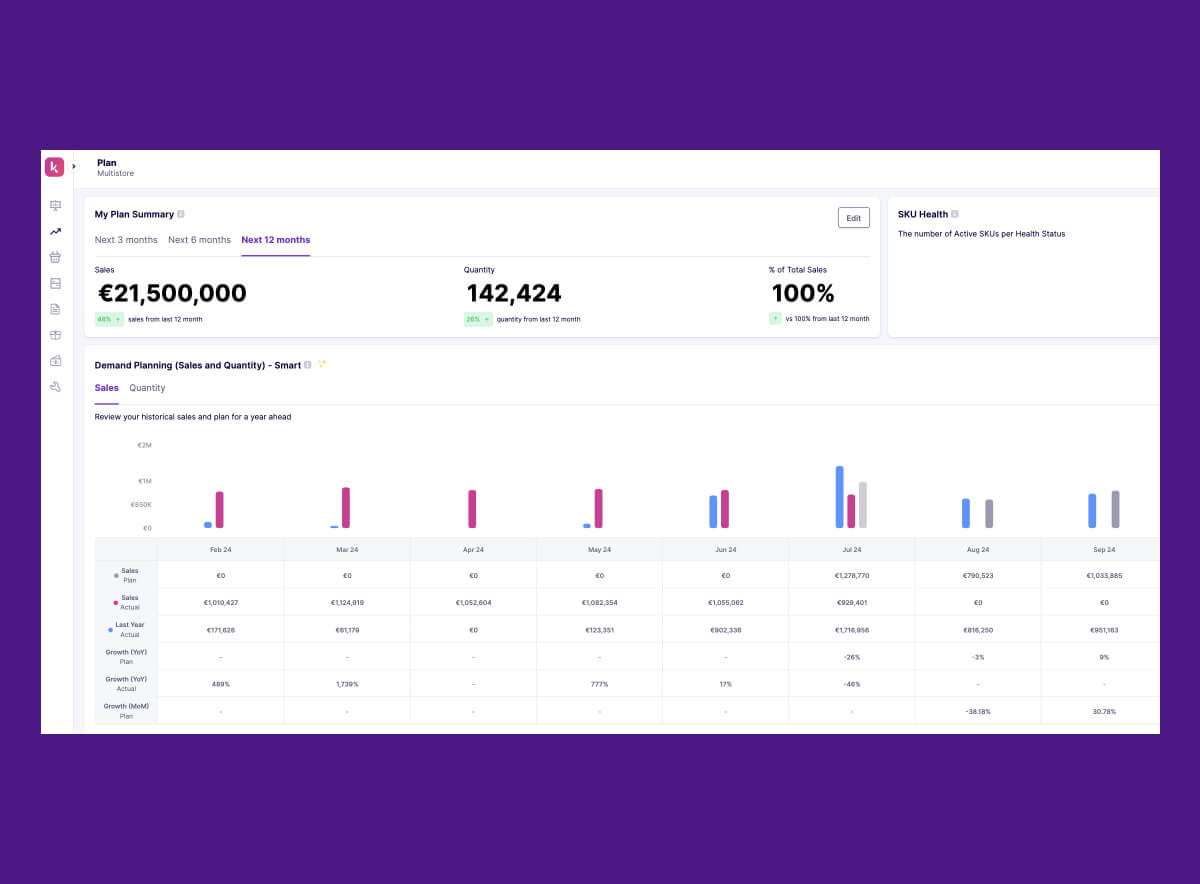
3. Integrated Data Analytics: Prediko combines various data points, including historical sales data, production schedules, and market trends, to generate accurate demand forecasts. This data-driven approach allows businesses to make informed decisions about inventory management, optimizing order quantities and reducing excess stock. The in-depth reporting and analytics provide valuable insights into inventory performance and trends, helping businesses identify cost-saving opportunities.
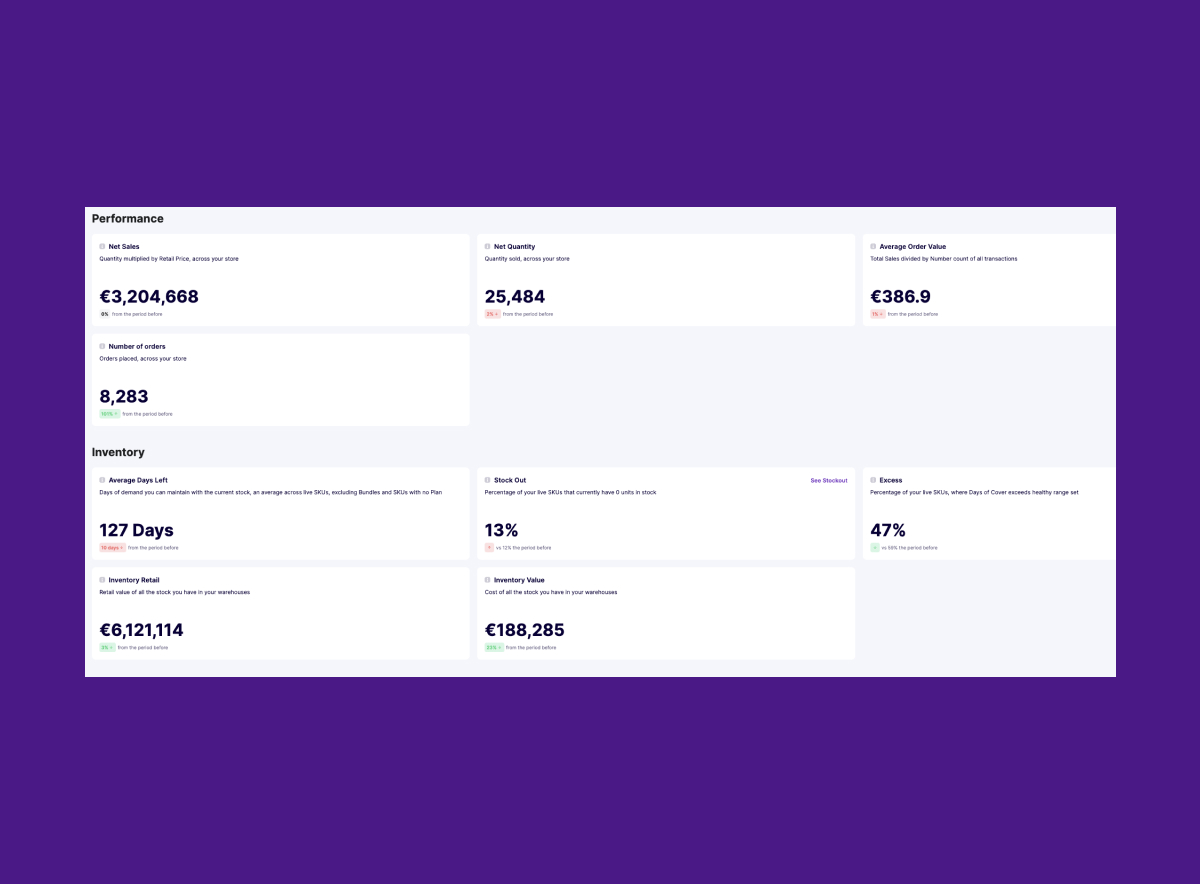
4. Cost reduction and efficiency: Prediko automates routine inventory management tasks, such as tracking stock levels, creating purchase orders, and updating records. This automation reduces the burden on staff and minimizes errors, leading to increased efficiency and cost savings. The detailed reports and analytics help businesses optimize their order quantities, reducing excess stock and minimising storage costs.
5. User-friendly interface: Prediko’s platform is designed with a user-friendly interface that makes it easy for all users to navigate and utilize its features effectively. This ensures that businesses can quickly adopt the software and start benefiting from its capabilities without a steep learning curve.
6. Scalability: Prediko is designed to handle complex operations and scale with your business. Whether you're managing a small or large inventory, the software can accommodate your needs, providing reliable support as your business grows.
7. Supplier Management: Prediko also offers tools for managing supplier relationships. By tracking supplier performance and lead times, businesses can ensure that they receive high-quality materials on time, supporting consistent production and maintaining product quality.
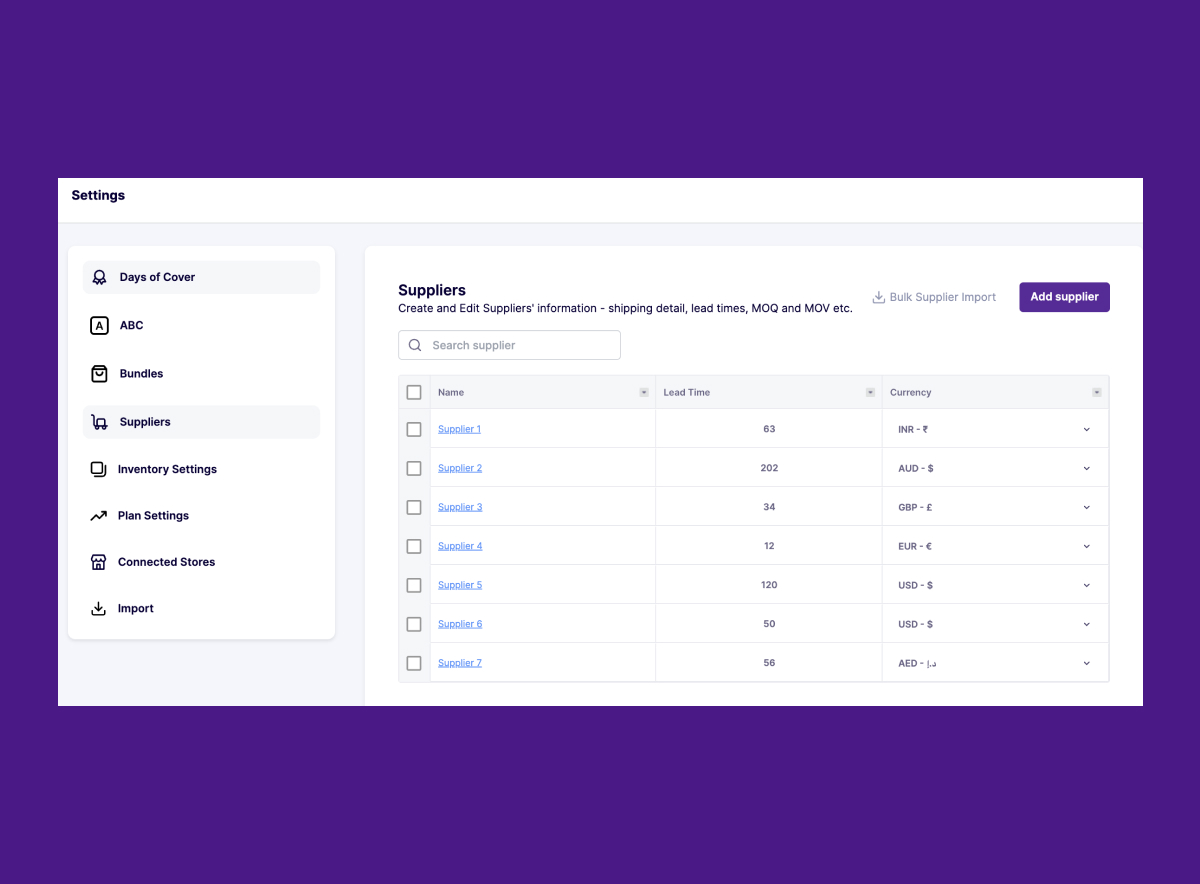
By leveraging these features, Prediko helps Shopify brands overcome common challenges in raw material inventory management, leading to improved efficiency, cost savings, and better overall performance.
Calculating & recording raw material inventory
Calculating and recording raw material inventory is a key aspect of raw materials management. This involves determining the quantity and value of materials on hand. This process is crucial for financial reporting. It affects the calculation of cost of goods sold, gross profit, and net income. Learn how to identify and calculate direct raw materials to be used for D2C brands.
Moreover, an accurate calculation and recording can provide valuable insights. It helps businesses identify trends, spot inefficiencies, and make informed decisions. However, this process could be complex. It involves various methods and techniques, each with its own pros and cons.
Learn how you can calculate direct raw materials cost for your Shopify brand. In addition, it requires meticulous record-keeping. Errors or discrepancies can lead to inaccurate financial reports and potential regulatory issues.
How to compute raw materials inventory
There are several methods for computing raw materials inventory. One of the most common is the First-In, First-Out (FIFO) method. This assumes that the first materials purchased are the first ones used in production. Learn how to use FIFO to calculate your inventory.
Another method is the Last-In, First-Out (LIFO) method. This assumes that the last materials purchased are the first ones used. Learn how to use LIFO to calculate your inventory. There's also the weighted average method. This calculates the average cost of all the materials on hand, regardless of when they were purchased.
Tracking raw materials inventory- Get techniques and tools
Tracking raw material inventory is an important part of the process. This involves monitoring the movement of materials from receipt to use in production. Tracking raw materials helps in preventing stockouts and overstocking. These tools can also provide valuable data for forecasting and decision-making.
However, tracking raw material inventory is challenging. This requires a system that can handle large volumes of data and provide real-time updates. Fortunately, there are various techniques and tools available. These include barcode scanning, RFID technology, and inventory management software.
These tools can automate the tracking process, reduce errors, and provide real-time visibility into inventory levels.
How to effectively track raw materials within Shopify
To effectively track raw materials in Shopify, you can utilize inventory management apps or tools that integrate with Shopify. These tools can help you monitor the quantity of raw materials you have on hand, set up alerts for low stock levels, and track the movement of materials in and out of your inventory.
By maintaining accurate records of your raw materials, you can optimize your production processes, reduce waste, and ensure that you always have the necessary materials on hand to fulfill orders.
Real-time tracking within Prediko and its advantages
Within Prediko, you get a real-time update on how many raw material units you currently have in stock, how many units are in transit and how many units are in production. By knowing exactly what materials are on hand, businesses can plan production schedules more effectively.
Moreover, real-time tracking can support better decision-making. This provides accurate, timely data that can be used for forecasting, budgeting, and strategic planning.
Setting reorder points and economic order quantities
Setting reorder points and economic order quantities is another important aspect of raw material inventory management. Reorder points determine when new orders should be placed, while economic order quantities determine how much should be ordered.
How does setting up this work in Shopify?
Once your Shopify store installs Prediko's app, they don't have to set reorder points and economic order quantities. Prediko's Buying Table analyzes your existing inventory levels and shares in an interactive way on when to order and how much to order.
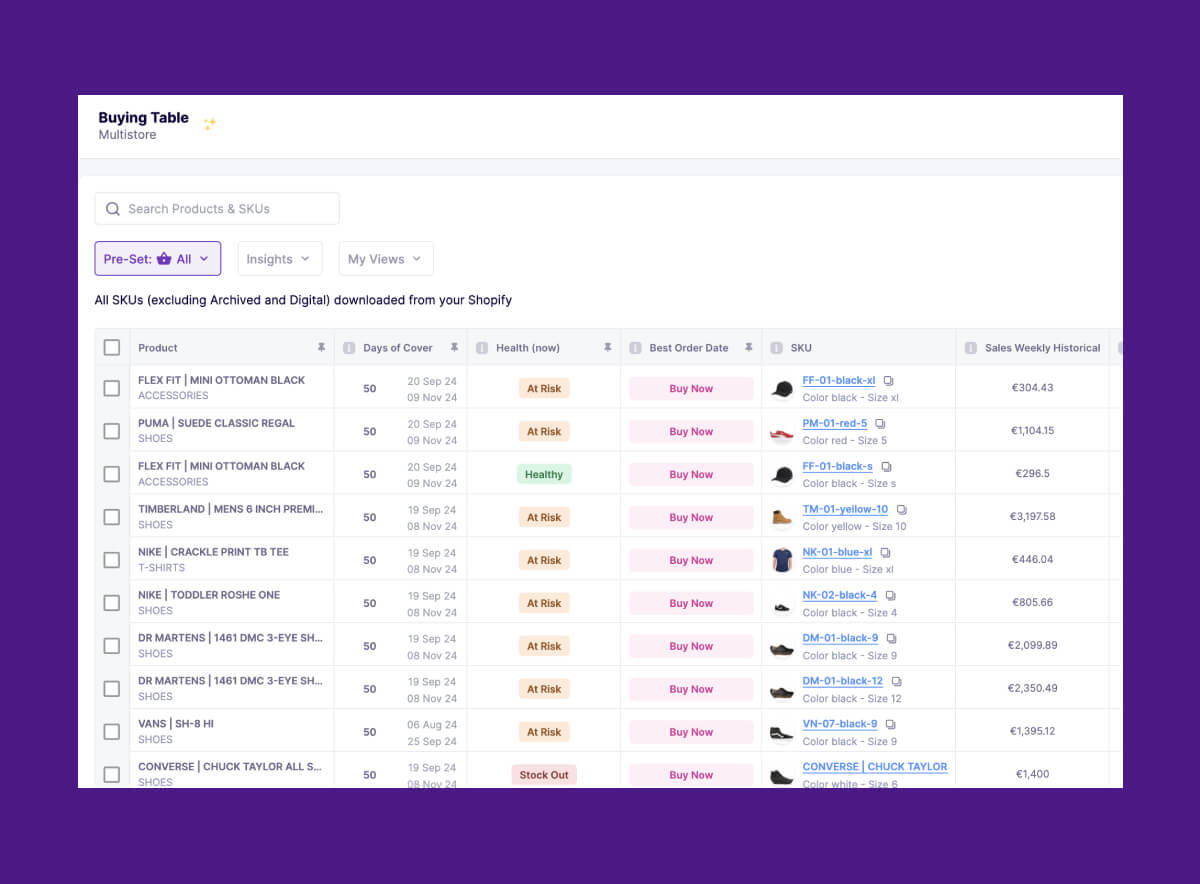
They ensure that businesses have the right amount of materials on hand at the right time. Setting these metrics requires careful analysis. Businesses need to consider factors like lead times, demand patterns, and storage costs to determine the optimal reorder points and order quantities.
Calculating Raw Materials Inventory Turnover
The raw materials inventory turnover ratio gauges how effectively a company utilizes its raw materials in manufacturing. To determine this ratio, you need the following data:
Cost of Goods Sold (COGS): This represents the total cost of raw materials consumed in production over a specific period, encompassing materials that were converted into finished products.
Average Raw Materials Inventory: This is calculated by adding the raw materials inventory at the beginning of the period to the inventory at the end of the period and dividing by two. This calculation provides the average inventory value for that timeframe.
With these values in hand, the formula to calculate the raw materials inventory turnover is:
Raw Materials Inventory Turnover = COGS / Average Raw Materials Inventory
The resulting figure indicates how many times the company’s raw materials inventory is cycled through and replaced within the given period. A higher turnover rate signifies efficient material usage, whereas a lower rate may point to overstocking or production inefficiencies.
Future trends in raw material inventory management
The future of raw material inventory management is promising, with several trends and innovations on the horizon. Predictive analytics, IoT integration, and blockchain technology are here to revolutionize inventory management.
- Predictive analytics and demand forecasting: AI and machine learning technologies can analyze data to predict future demand and optimize inventory levels.
- Blockchain for transparency and security: Blockchain technology can enhance transparency and security by providing a secure, decentralized record of transactions, reducing the risk of fraud and errors.
Also read: A Complete Guide to Shopify Inventory Management
Impact of software on raw material inventory management
Investing in the right raw material inventory management software can bring significant benefits, including streamlined processes, reduced errors, and valuable insights.
It enhances visibility and control over inventory, helping businesses avoid overstocking and stockouts while facilitating compliance with industry regulations.
Ultimately, such an investment can optimize inventory management processes, improve the bottom line, and maintain competitiveness in the market.