Production halts, missing components, unexpected cost spikes, wasted resources, and frustrated customers are just some of the consequences of mismanaging your bills of material.
Trust us, things can get even worse.
This is why having a solid Bills of Material (BOM) inventory management process is important. It ensures you’re always prepared, with every component accounted for and your production running smoothly.
This article will cover everything you need to know about BOMs, including the different types, a step-by-step process to manage them, common challenges you might face, and a review of the top 5 software for BOM management.
What is the Bill of Materials in Inventory Management?
A Bill of Materials (BOM) is a detailed list of all the parts, materials, and subassemblies needed to make a product. It also includes information like quantities, costs, lead times, and part numbers. Simply put, it’s the blueprint to turn raw materials into a final good.
The Bill of Materials (BOM) for a wooden table could look something like this
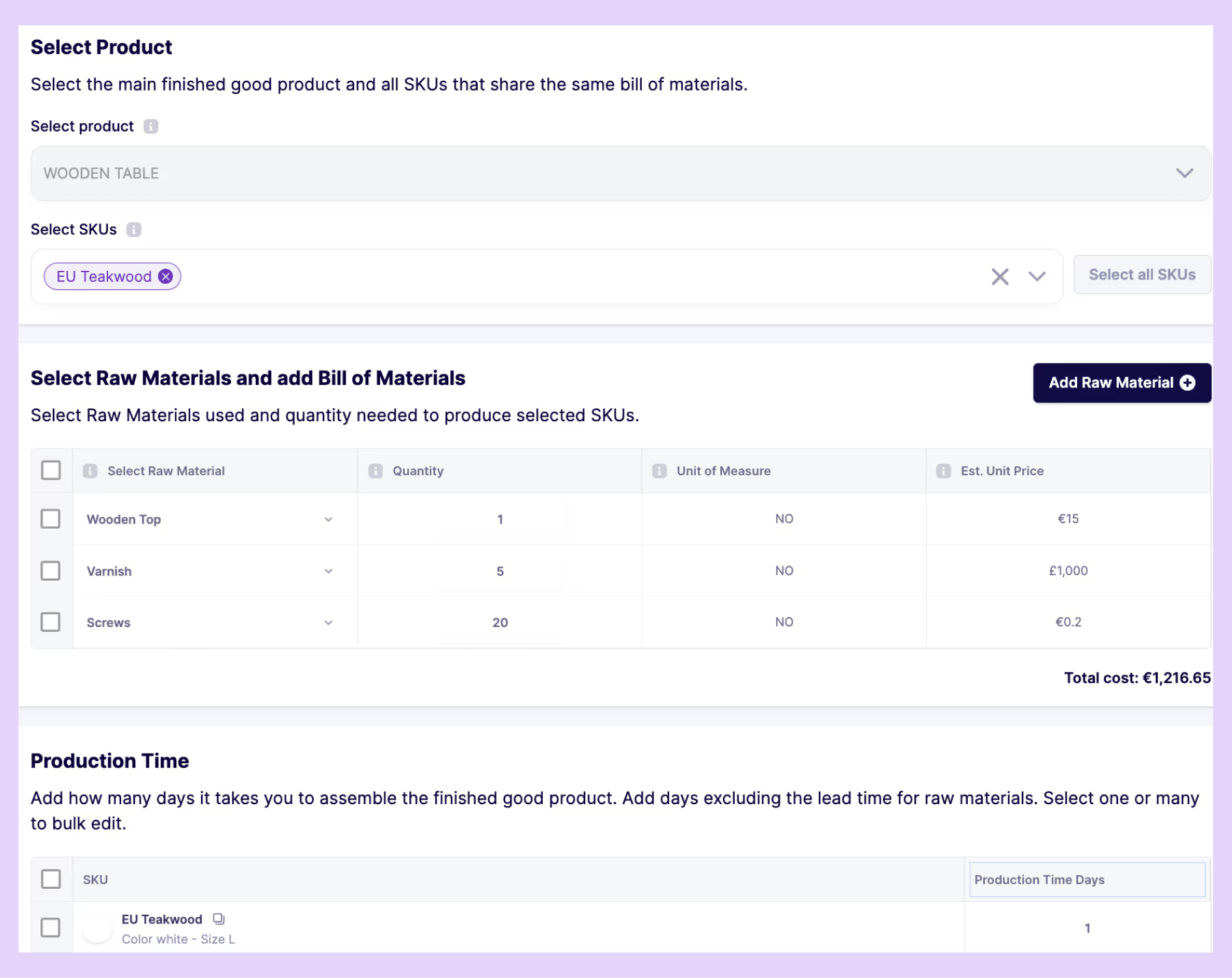
This BOM details the components (wooden top, screws, varnish), the quantities required, unit costs, and total costs for each part of the table. This helps manufacturers understand exactly what is needed to produce the table, along with the total production cost. It also provides a part number for tracking and reordering components.
Why is BOM Management Important?
By maintaining detailed BOMs of all components, raw materials, quantities, and their associated costs
- Minimize excess inventory and stock outs by knowing exactly how many components you will need for each production cycle
- Accurately calculate product costs, forecast future expenses, and identify areas for cost-cutting
- Better negotiate with vendors through accurate and predictable order volumes
- Eliminate production delays and accurately schedule manufacturing runs with on-time availability of components
- Maintain product quality and compliance by tracking and documenting every component used in production
- Expedite the product development cycles with error-free and smooth production. Reduce time-to-market and execute product launches faster
- Improve coordination among various departments (engineering, procurement, production) with BOMs acting as a shared reference
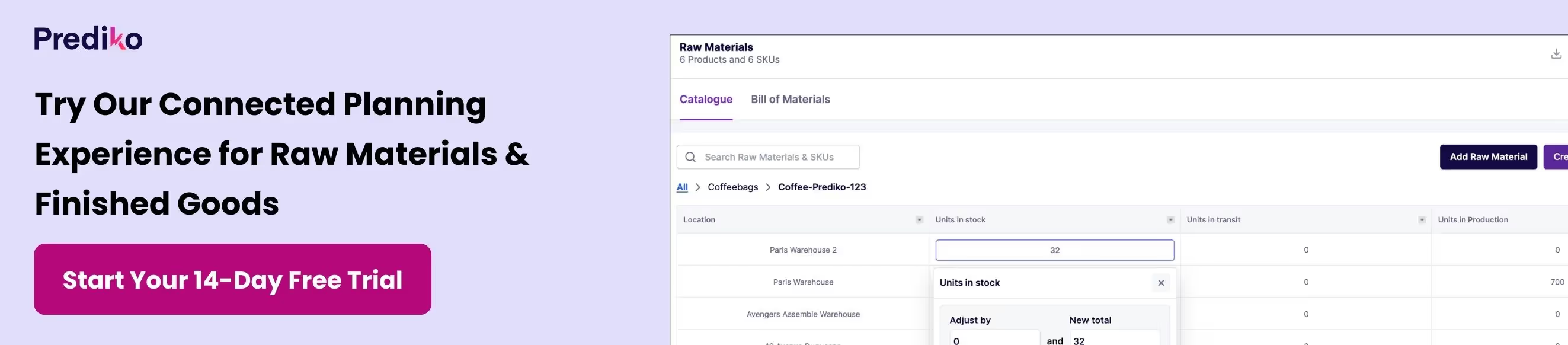
Types of Bill of Materials
There are different types of BOMs and each serves a distinct purpose. Understand the differences and choose the right BOM type based on factors like product complexity, customizations, and your manufacturing process.
1. Single-Level BOM
A Single-Level BOM, also known as a flat BOM or level-0 BOM, is the simplest form of materials listing. It represents all components and their quantities needed for a finished product in a single, non-hierarchical format. This is best suited for simpler products.
A basic wooden table will have a single-level BOM that lists individual components like wood, nails, paint, and screws but doesn't involve any assembly beyond the basic construction.
This type of BOM is particularly great for simple products where only a few components come together in a straightforward assembly process. However, this simplicity can become a limitation when dealing with more complex products.
2. Multi-Level BOM
A Multi-Level BOM (aka hierarchical BOM) is used for more complex products that consist of multiple sub-assemblies, parts, and raw materials. It gives a complete view of product structure by showing parent-child relationships between components.
This helps understand how different parts come together to form sub-assemblies, and how these sub-assemblies ultimately create the final product.
Commonly used in complex manufacturing industries like automotive and electronics, a Multi-Level BOM breaks down products like a car into sub-assemblies, such as the engine, chassis, and interior, further breaking down the components of each.
3. Configurable BOM
A Configurable BOM is ideal for products that offer multiple variations or customization options or made-to-order processes. This BOM type allows manufacturers to configure the components, materials, and parts based on customer preferences, such as color, size, or features.
It is particularly useful in mass customization, made-to-order, or build-to-order processes where each unit or batch may have different configurations.
Computer manufacturing may have a configurable BOM to adjust component requirements based on customer choice for processor type, memory capacity, storage options, and display specifications.
4. Engineering BOM (EBOM)
An Engineering BOM is created during the product design phase and includes the technical specs, material requirements, design parameters, and CAD file references. This type of BOM is important for product development and engineering teams to translate the conceptual design into an actual product.
Unlike other BOM types, the EBOM focuses more on the design part rather than production or assembly.
5. Manufacturing BOM (MBOM)
A Manufacturing BOM is tailored for production needs. This is used by production teams and focuses on the materials and components required for the assembly and manufacturing of the product. It includes all the components listed in the EBOM but also adds production-specific details such as assembly steps, tools, packaging, and any special instructions.
The MBOM is essential for production managers and shop floor workers, providing them with all relevant information to efficiently manufacture the product while maintaining quality standards.
A manufacturing plant producing a television would have an MBOM that lists all components like the screen, electronics, casing, screws, and packaging materials along with assembly instructions.
Common Challenges in BOM Management
As you step into the complex process of managing Bills of Materials, some issues are bound to surface. Here are the most common challenges, along with actionable strategies to overcome them.
Typical obstacles & inefficiencies
Managing BOMs involves handling complex information like detailed component lists, quantities, costs, etc. A single error, such as an incorrect part number or missing materials, can lead to major production disruptions.
Inconsistent communication between teams can also lead to inaccurate supply of raw materials and delays. Manual data entry is another major setback that makes BOM management on Shopify prone to human errors and slows down updates.
Solution: Conduct regular BOM audits to check for inconsistencies and data accuracy. Set up a structured process for BOM updates. You can establish clear guidelines and a checklist for creating and updating BOMs.
Prediko allows you to import material lists and make them readily accessible along with your final goods inventory, giving your team a single view of both raw materials and finished products. This results in more accurate planning and execution.
Keeping BOMs updated
Products undergo revisions over time based on customer needs. As designs evolve or suppliers change, keeping the BOMs updated gets difficult. This leads to issues like the wrong materials being used or delays in production while waiting for the right components.
Solution: Automate change notifications to relevant departments whenever a component is revised. Schedule routine BOM reviews, especially when a design change or new version is introduced.
Use a tool like Prediko that allows you to easily update BOMs as product requirements change, quickly assess the impact of modifications, and keep all stakeholders on the same page
Managing multiple BOMs across product lines
If your company manufactures different products or variants, managing separate BOMs can lead to confusion and overlap, especially if common components are used. Products with different variants make the process even more complex. Mismanagement can affect multiple production schedules and increase inventory costs.
Solution: Build templates and reusable sub-assemblies to quickly create new BOMs for similar products. Deploy an inventory management software like Prediko that allows you to assemble detailed BOMs for each product across multiple warehouses, locations, and product lines on one dashboard. This helps manage storage and distribution.
Integrating BOM data across ERP systems
BOM data is often managed separately and needs to be connected with ERP, MRP, or inventory management apps. Lack of integration creates data silos where information is scattered across various platforms and departments, making it hard to maintain a single source of truth. This can cause order errors, skewed inventory records, or even financial mistakes.
Solution: Choose an inventory management software with bills of materials management capabilities or integrations for managing inventory and related processes. Look for tools that offer native integrations or, at least, support API connections.
Prediko’s inventory management solution has in-built BOM management features, giving your team a single view of the entire supply chain, from raw materials to finished goods.
Implement Effective BOM Inventory Management
Follow this step-by-step approach to create a solid and reliable BOM inventory management system that supports your operational goals.
Step 1: Standardize BOM structures across departments
The BOM inventory management process begins with creating a BOM template (use Google Sheets) that includes key details such as part numbers, detailed descriptions, required quantities, sourcing data, and a complete revision history.
Maintain standardization in naming conventions such as PP-001 for purchased parts and MA-001 for manufactured assemblies. Also, clearly define which fields are mandatory and which are optional. Document the creation process for reference across departments or new team members.
Step 2: Choose an inventory management system that supports BOMs
Next, select an inventory management system that accommodates multi-level BOMs and also provides real-time finished goods inventory tracking.
Jot down the detailed requirements and specific needs of the company. Go for a cloud-based solution. Then, engage with multiple vendors and request detailed demos from at least 3-5 potential providers. Include IT, production, and engineering teams in the selection process to consider all perspectives.
If you’re a Shopify store owner, Prediko is a perfect choice as it combines both raw materials and finished goods tracking across your supply chain with its extensive inventory management and BOM features.
Step 3: Train staff on BOM maintenance & updates
Develop an exhaustive training program that covers important BOM management concepts, like system-specific features, detailed data entry rules, change management processes, team/department roles, and quality control protocols. Also include common tips and mistakes to avoid.
Use actual examples from your company's operations to make the training more relevant and practical. Record all training sessions and create a library of resources to be accessed in the future.
Step 4: Integrate BOM with real-time inventory tracking
Now that you have a system in place to view both raw materials and finished goods on one interface, make sure to sync the BOM data with real-time inventory tracking. This will help improve production planning, procurement, and order fulfillment.
Step 5: Implement regular audits & updates for BOM accuracy
Regular audits and updates are a must for accurate BOM inventory management. Establish a detailed audit schedule that includes weekly data accuracy checks, monthly inventory reconciliation, quarterly BOM reviews, and annual full audits.
Keep verifying supplier information and cost in the audit processes. Create detailed audit checklists and rotate audit responsibilities among team members for fresh perspectives and objectivity.
Prediko lets you update and modify the Bills of Materials(BOMs) as needed, ensuring your production line stays on track.
if you have more questions, you're not alone. Get answers to the 5 most pressing inventory questions from the Limited Supply Podcast in this article.
Best Practices for Optimizing BOM Management
To produce and manage your BOMs efficiently, it's important to keep in mind the following practices.
Automate processes and integrate tools
Integrate your BOM solution with ERPs to centralize data and sync BOM management with other critical functions such as procurement, production planning, sales forecasting, and financial reporting. This centralization makes the right materials and resources available when needed.
Moreover, manual processes like entering part numbers, quantities, or updating versions are error-prone and time-consuming. Relying on them can be costly. Automation pulls accurate data from integrated sources so that your BOMs are always up-to-date and all stakeholders (internal teams and external suppliers) are working with the correct information.
If possible, look for inventory management software that can do BOM management along with finished goods so that a seamless flow of data can be created.
Prediko is an inventory management software for Shopify brands that lets you manage almost every aspect of your supply chain, from finished goods inventory and raw material tracking to purchase order management and sales forecasting.
Monitor Data in Real-time
Live data is important if you are executing the just-in-time inventory management strategy, where the stock arrives as it is needed for production.
Relying on outdated or batch-processed information can result in stockouts or excess inventory, both of which can be costly. Real-time monitoring lets you make quick, informed decisions and have the right materials on hand at the right time.
It also helps you spot issues well in advance like discrepancies in inventory levels, overdue orders, or delays in the supply chain before they become bigger problems.
Document and standardize processes
Without standardized processes, different departments may manage the BOM in different ways, leading to confusion and inconsistency.
Begin by creating a master template or SOP that defines mandatory fields, naming conventions, and clear approval workflows. It should specify exact procedures for BOM creation, updates, and version control. This SOP allows all teams, whether in procurement, production, or inventory management, to be on the same page.
Give relevant members from each team access to BOM management software and establish team communication channels, if necessary. You may also create video tutorials that walk employees through the procedure of BOM management.
Do Forecasting and Demand Planning
Preplan your raw materials inventory and demand to avoid over-ordering materials or running into shortages. Use historical data, market trends, customer order patterns, and production schedules to forecast demand for raw materials and components.
The more accurate your forecasts, the better you can plan your BOMs to meet production needs without excess waste. Plus, using the BOM for production planning ensures that you have the exact parts needed for each phase of production.
Choosing Right Software for BOM Inventory Management
Manually managing BOMs is not an effective approach and gets difficult as your production scales. To maintain accuracy, efficiency, and seamless communication across departments while managing BOMs, it’s important to make use of technology.
A dedicated BOM software can simplify key stages in BOM management including updating and managing the BOMs, integrating these with other processes, and forecasting demand.
Choosing the right software brings you a step closer to an optimized production process.
Here are the key features you must look for in a BOM inventory management software
1. Real-time inventory tracking
Choose a solution that gives you real-time visibility into current inventory levels across multiple locations. This enables you to track stock as it’s received, used in production, or transferred, preventing discrepancies and supporting quick decision-making.
2. Multi-level BOM support
The software should also offer multi-level BOMs for complex product structures with hierarchical component relationships. This feature allows you to precisely track both parent and sub-assemblies, providing a complete and detailed view of the production needs.
3. Integration capabilities with other tools (ERP, CRM)
Ensure the platform integrates with other business tools, such as ERP and CRM for seamless data flow between them. Integrations eliminate manual data entry and provide a unified view of business operations across different tools.
4. Customizable fields and flexible BOM management
The tool must offer configurable templates and field options to accommodate unique industry or company-specific requirements. With such a feature, you can easily modify BOMs, support version control, and quickly adapt to design changes or product variations.
5 Popular BOM Inventory Management Tools for Shopify Stores
Now that you understand the key features to look for in a BOM inventory management software, here are five popular options to consider.
No.1 👉 Prediko's AI Inventory Management App
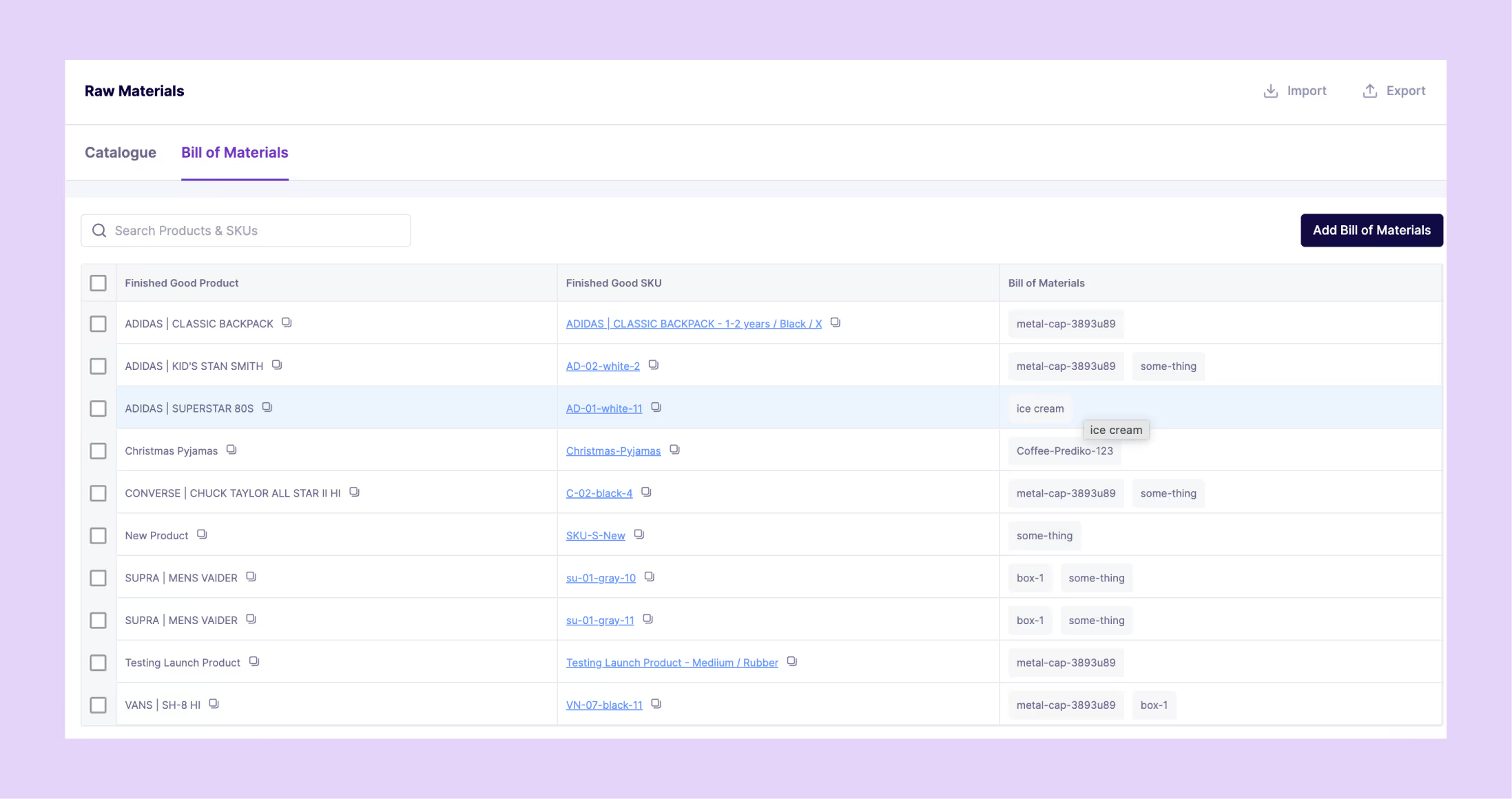
Prediko is a full-fledged inventory management solution that enables you to plan and manage both finished goods and raw material inventory simultaneously.
You get a unified dashboard to track and oversee all aspects of your supply chain– Raw materials, BOMs, purchase orders, finished goods inventory, and even sales forecasts. Its seamless integration with Shopify makes it a great choice for Shopify stores dealing with complex production workflows.
Key features
- Import raw material data: Fetch your entire raw material data in bulk with a single import and easily manage your inventory.
- Multi-warehouse support: Optimize storage and distribution by managing raw materials across multiple locations.
- BOM creation and tracking: Quickly create detailed BOMs for each product and update them as needed to ensure production runs smoothly.
- Made-to-stock production orders: Create made-to-stock production orders to keep inventory levels ready to meet demand without overproducing.
- Demand planning for raw materials: Prepare for future inventory needs by forecasting the raw materials required to meet production and customer demands. (coming soon)
- Finished goods inventory management: Plan and manage finished goods inventory with AI-powered forecasting, buying table, automated suggestions, inventory reports, and purchase order creation.
Pricing
Prediko offers three pricing plans; Starter at $119/month, Growth at $199/month, and Enterprise at $349/month. All plans include the same core features, with plans varying based on your business's revenue volume.
2. Katana
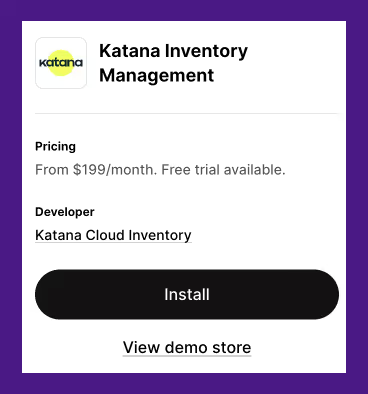
Katana is a comprehensive inventory software that helps businesses manage everything from from purchase of raw materials to the delivery of finished goods across multiple sales channels.
Key features
- Real-time data for production planning
- Made-to-order and made-to-stock workflows
- Supports the creation of multi-level and single-level BOMs
- Automated manufacturing cost calculations
- Shop floor app to access real-time shop floor insights
Pricing
Plans start at $179 per month, billed annually.
3. MRPeasy
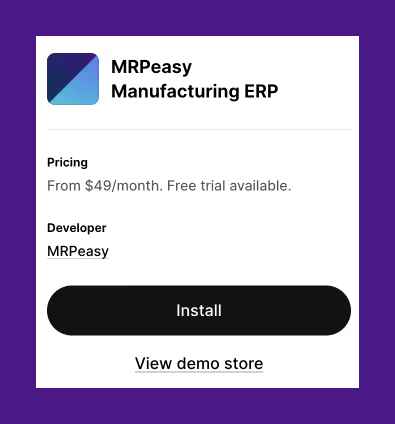
MRPeasy is a material requirements planning software specifically designed for small to medium-sized manufacturers and distributors, typically with 10 to 200 employees. It adds efficiency and brings together various aspects of manufacturing operations.
Key features
- Single-level and multi-level BOMs creation along with CSV uploads
- Matrix BOM functionality to configure products
- Automatically calculates order costs and checks material availability.
- Scheduling of manufacturing and purchase orders
- Integrations to manage production planning, inventory, sales, and more in one place
- Version control system to record changes in your BOMs
Pricing
Plans start at $49 per month.
4. Unleashed inventory management
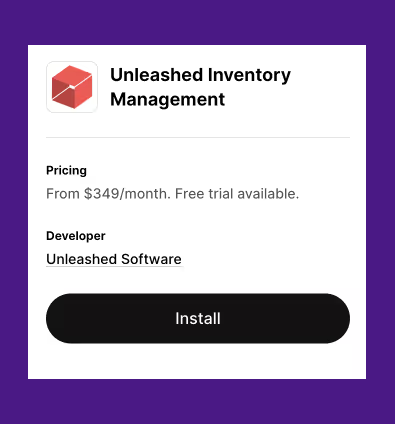
Unleashed is an inventory management tool designed for retailers, manufacturers, wholesalers, and distributors. It provides control over stock levels, production, and purchasing processes, enabling you to operate proactively and efficiently.
Key features
- Manage multi-level Bills of Materials
- File library to manage all the production documentation
- Stock ordering for production based on your BOMs and existing inventory
- Disassembly for selling individual products
- Build kit sets or bundles on the fly
- Automated calculations of production costs to see precise profit margins
Pricing
Plans start at $349 per month.
5. Craftybase
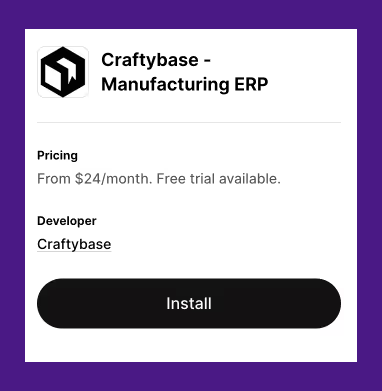
Lastly, we have Craftybase, which simplifies inventory management for small manufacturers by allowing them to easily generate accurate BOMs in minutes. It helps businesses track materials and update BOMs as needed, ensuring they always know exactly what’s needed for production.
Key features
- Create and manage complex multi-level BOMs
- Track both raw materials and finished products
- Automated calculations for inventory and COGS
- Easily forecast and schedule production requirements
Pricing
Plans start at $24 per month.
Prediko’s inventory management solution stands out with its extensive and powerful BOM management features. Think it can fit right into your business operations? Start a free 14-day trial now and see for yourself.